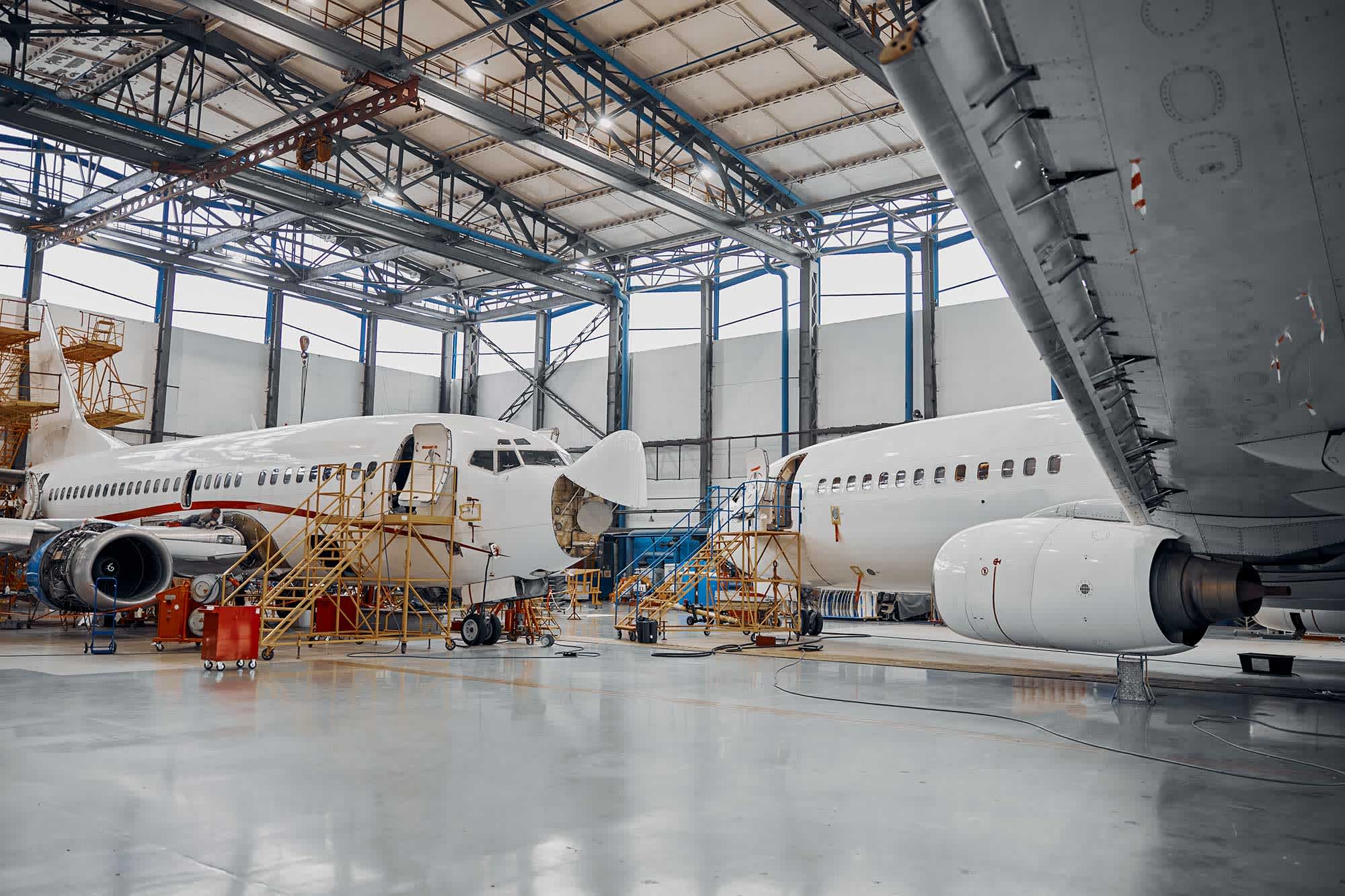
Mitigating Aerospace Supply Chain Disruptions: A Simulation-Driven Approach
Published: Mar 05 2025
Imagine a jetliner grounded, not because of a mechanical failure, but because a tiny part, crucial for its navigation system, is stuck halfway across the world. This isn't a hypothetical scenario; it’s the reality of supply chain disruptions in the aerospace sector. These disruptions, occurring with alarming frequency, can have a devastating impact, costing millions in lost revenue and delaying critical projects. The aerospace manufacturing industry faces unique challenges, from long lead times for specialized aerospace parts to complex global supply networks and stringent quality requirements.
This article explores how simulation, a powerful analytical tool, can model, predict, and ultimately help develop proactive strategies for these disruptions, ensuring your business stays airborne. Design Systems, Inc., with its extensive experience, stands at the forefront of this innovative approach.
Understanding the Current Landscape of Aerospace Manufacturing
What is going on in the aerospace manufacturing industry? It's a complex picture. Global supply chains are more intricate than ever, with components sourced from all corners of the world. This interconnectedness, while offering benefits, also creates vulnerabilities. Geopolitical events, economic fluctuations, and rapid technological advancements can all send shockwaves through the system. Consider the impact of a natural disaster on a key supplier or a sudden surge in demand for a specific type of aerospace parts. These events can create bottlenecks, delays, and even complete shutdowns. Aerospace manufacturers, the linchpins of this ecosystem, must navigate these challenges effectively to maintain production and meet customer demands. Consider these key aspects:
Globalization and Complexity: Aerospace supply chains span the globe, involving numerous suppliers, each with their own unique challenges and dependencies. This intricate network increases the risk of disruptions at any point along the chain.
Long Lead Times: The aerospace industry often deals with long lead times for specialized parts, sometimes stretching several months or even years. This makes it difficult to react quickly to unexpected changes in demand or supply.
Stringent Quality Requirements: Aerospace parts must meet extremely high quality and safety standards. This necessitates rigorous testing and certification processes, which can further complicate and lengthen the supply chain.
Technological Advancements: Rapid advancements in aerospace technology require manufacturers to constantly adapt their supply chains to incorporate new materials, processes, and components. This can create challenges in finding reliable suppliers and integrating new technologies into existing systems.
Geopolitical Instability: Global events, such as trade wars, political instability, and pandemics, can significantly disrupt supply chains, impacting the availability of critical parts and materials.
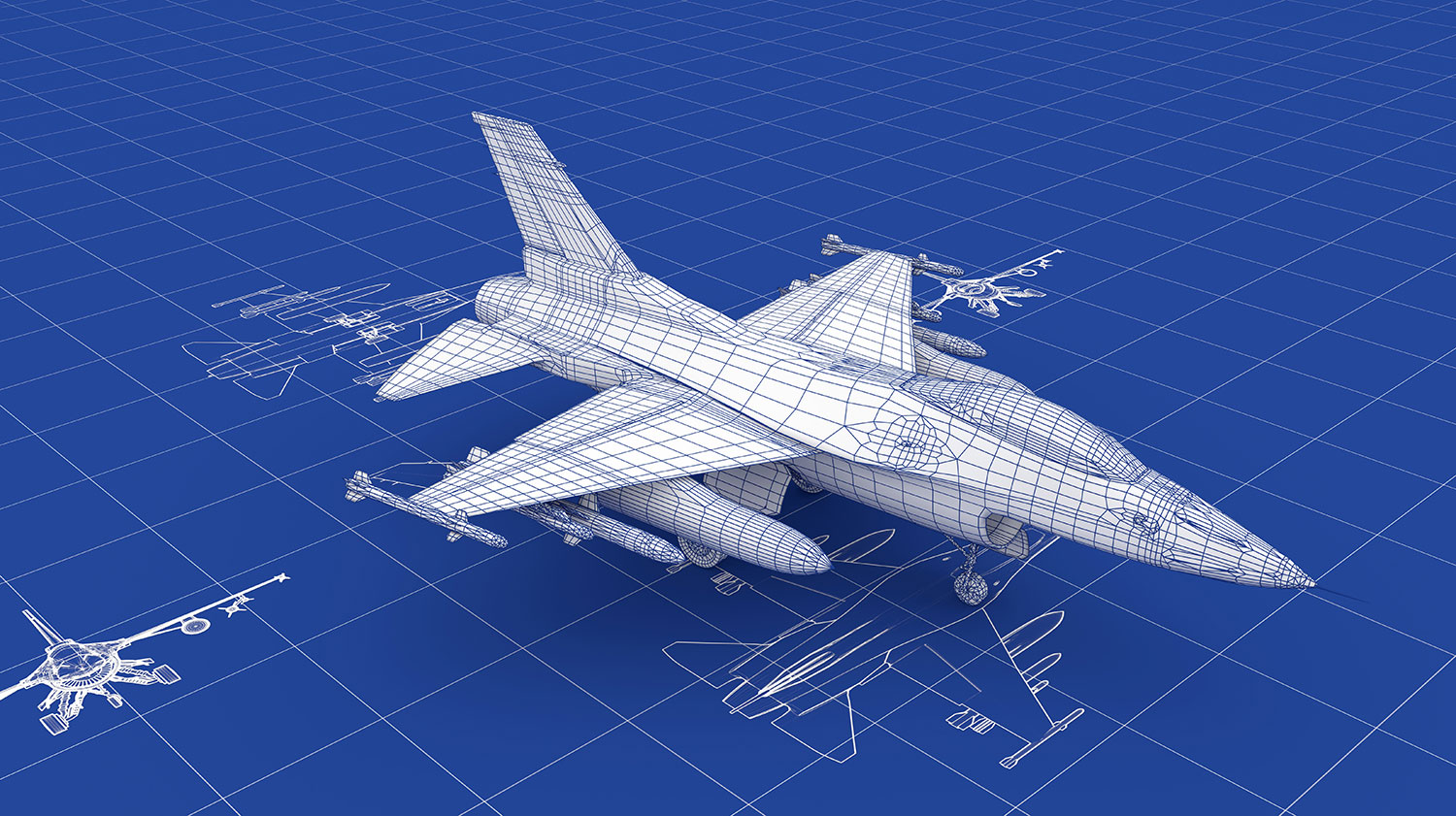
The Role of Simulation in Mitigating Supply Chain Disruptions
Simulation engineering provides a virtual laboratory for understanding and optimizing complex systems. It involves creating a digital representation of your supply chain, including suppliers, manufacturing processes, and logistics.
Different types of simulation models, such as discrete event simulation, can be used to analyze various scenarios. The benefits are substantial. Simulation allows for proactive risk assessment, identifying vulnerabilities before they become real problems. It enables testing different scenarios, like a sudden increase in demand or a supplier going bankrupt, and evaluating their potential impact.
Inventory levels and production schedules can be optimized, minimizing costs and maximizing efficiency. Furthermore, simulation fosters improved collaboration and communication among supply chain partners, creating a more cohesive and resilient network. Imagine simulating the impact of a port closure on your delivery schedules. By understanding the potential consequences, you can proactively develop alternative routes and minimize delays. Here's a closer look at how simulation helps:
Proactive Risk Assessment: Simulation allows you to identify potential vulnerabilities in your supply chain by modeling various disruption scenarios. This enables you to proactively develop mitigation strategies and minimize the impact of future disruptions.
Scenario Planning and Analysis: Simulation enables you to test different scenarios, such as changes in demand, supply disruptions, and transportation delays, and evaluate their potential impact on your operations. This helps you make informed decisions about inventory levels, production schedules, and resource allocation.
Optimization of Inventory and Production: Simulation can be used to optimize inventory levels and production schedules, minimizing costs while ensuring that you have sufficient resources to meet demand.
Improved Collaboration and Communication: Simulation can facilitate better communication and collaboration among supply chain partners by providing a shared understanding of potential risks and challenges.
Cost Reduction and Resilience: By identifying and mitigating potential disruptions, simulation can help reduce costs associated with delays, lost sales, and production downtime, while also improving the overall resilience of your supply chain.
A Simulation-Driven Approach to Aerospace Supply Chain Resilience
Building a resilient aerospace supply chain requires a structured, simulation-driven approach. First, robust data collection and analysis are crucial for building accurate simulation models. The more information you have about your suppliers, their capacities, and their lead times, the more realistic and valuable your simulation will be.
Next, identify the critical points in your supply chain that are most susceptible to disruptions. These could be single-source suppliers, geographically concentrated production facilities, or bottlenecks in your logistics network.
Once these vulnerabilities are identified, develop and test various mitigation strategies using simulation. For example, you might simulate the impact of diversifying suppliers, building buffer stock, developing alternative transportation routes, implementing agile manufacturing processes, or improving communication and collaboration with existing suppliers.
Simulation engineering allows you to evaluate the cost-effectiveness and feasibility of each strategy before implementing it in the real world. Continuous monitoring and improvement are essential. Regularly update your simulation models with new data and refine your mitigation strategies as needed. This process typically involves the following steps:
Data Collection and Analysis: Gather comprehensive data on your supply chain, including supplier information, lead times, transportation routes, inventory levels, and production schedules.
Vulnerability Assessment: Identify critical points in your supply chain that are most susceptible to disruptions, such as single-source suppliers, geographically concentrated production facilities, or transportation bottlenecks.
Model Development: Create a simulation model of your supply chain that accurately reflects its structure, processes, and dependencies.
Scenario Testing: Run various scenarios through your simulation model to evaluate the potential impact of different types of disruptions, such as supplier failures, transportation delays, and demand fluctuations.
Mitigation Strategy Development: Develop and test various mitigation strategies using simulation, such as diversifying suppliers, building buffer stock, or implementing agile manufacturing processes.
Implementation and Monitoring: Implement the most effective mitigation strategies and continuously monitor your supply chain to identify and address any emerging risks.
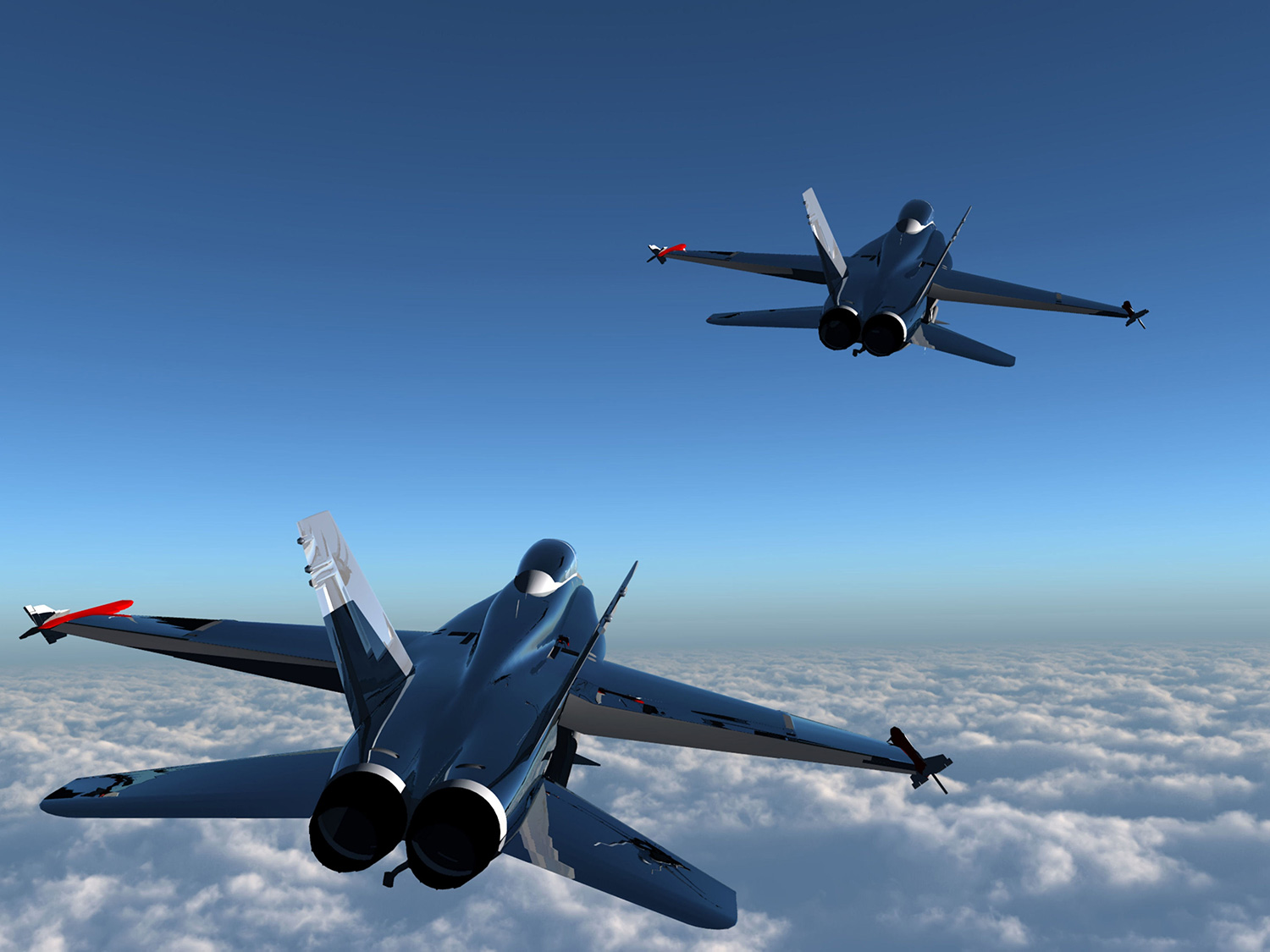
Design Systems, Inc.: Your Partner in Aerospace Supply Chain Resilience
The aerospace industry faces significant challenges regarding supply chain disruptions. Design Systems, Inc. understands these challenges and offers tailored solutions. Our expertise in simulation engineering and supply chain management enables us to help aerospace companies develop and implement simulation-driven solutions for mitigating supply chain risks. We offer a range of services, including supply chain modeling, simulation development, and expert consulting.
Contact us today for a consultation and let us help you build a more resilient and robust aerospace supply chain.
Conclusion
In today's interconnected world, supply chain disruptions are a constant threat. For the aerospace industry, the stakes are particularly high. Simulation engineering offers a powerful tool for understanding, predicting, and mitigating these risks. By embracing a simulation-driven approach, aerospace companies can build more resilient supply chains, ensuring they remain competitive and prepared for whatever the future holds. The future of supply chain management in the aerospace industry depends on proactive planning and a commitment to continuous improvement.
Key Takeaways:
Supply chain disruptions are a significant challenge for the aerospace industry.
Simulation provides a powerful way to model, predict, and mitigate these disruptions.
A simulation-driven approach involves data collection, vulnerability identification, and strategy testing.
Diversifying suppliers, building buffer stock, and improving communication are key mitigation strategies.
Design Systems, Inc. offers expert services in simulation engineering and supply chain management.